1.888.302.4875
ECS Eclipse News Archives January 2012
Mr. Fix It
January 23, 2012 (comments: 0)
An ECS Eclipse field service technician recently came across something that made us all cringe. A shear valve beneath a dispenser had been wedged permanently open with a wrench (see picture below). Why was the shear valve jerry-rigged like that? Well, it was probably jamming up and restricting flow at the dispenser. Whoever decided on the jam-it-open quick fix wanted to solve the problem without regard for larger consequences.
Perspective was lost in this situation. The shear valve is essential for compliance and for protecting your business and the environment. If a vehicle were to crash into a dispenser and sever the fuel line to the pump, a properly functioning shear valve would shut off the flow of fuel and prevent a major release. This wrench will negate the purpose of the shear valve and allow product to gush out onto the site in the event of dispenser dislodgement.
Which would be a greater loss to your business:
-A temporary shut off of one dispenser to repair the sticky shear valve,
or
-A collision with the dispenser causes a release, endangering customers and incurring thousands of dollars in clean up costs?
Bottom line: the equipment is there for a reason. Make sure it is working. Functioning compliance equipment is good for your business, good for your customers and good for the environment.
-Brian Yellan, ECS Eclipse Trainer
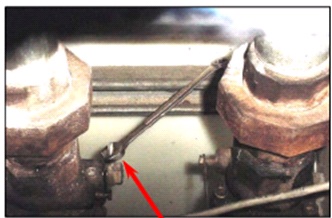
Daily Inventory Reconciliation
January 12, 2012 (comments: 0)
Did you know that the Ohio Bureau of Underground Storage Tank Regulations (BUSTR) effective earlier this year eliminated the requirement for monthly inventory reconciliation for UST systems? That’s right, the rule effective May 16, 2011 - O.A.C. 1307:7-9-07 - states that daily inventory control with monthly reconciliation is no longer required.
As required, a method of monthly release detection must be in place for all new and existing UST systems. However, in certain instances, inventory reconciliation can be temporarily used to meet the release detection requirements.
If the method of release detection becomes defective, the owner must immediately have the necessary repairs or maintenance performed. While the repairs are performed, the owner may use inventory control or automatic tank gauging (in the case where interstitial monitoring is the method of release detection) for up to 60 days from the last passing result in order to meet the monthly release detection requirements.
Additionally, if the automatic tank gauging system (ATG) is found to be not defective but a monthly passing release detection result cannot be acquired from the ATG due to low product levels in the tank, the owner may use inventory control as an alternative method of release detection for up to 90 days after the last passing result. Within that 90-day period, the owner is expected to schedule a fuel delivery in order bring the tank fuel level to the needed level.
To read the full rule – Release Detection Methods and Requirements for UST systems, follow this link:
http://codes.ohio.gov/oac/1301:7-9-07
-Megan Kazmierczak
Senior Compliance Manager
Northeastern US States move forward with Phase-out of Stage II Vapor Recovery
January 9, 2012 (comments: 0)
If your gasoline dispensing facility is subject to Stage II Vapor Recovery regulations, the remaining days for your Stage II vapor recovery system may be numbered. As you may have read or heard, some states have already changed their regulations to eliminate the requirement for Stage II Vapor Recovery.
The requirement for new vehicles in the USA to be equipped with On-board Refueling Vapor Recovery (ORVR) systems is leading to the elimination of Stage II Vapor Recovery requirements. To explain briefly, Stage II systems capture gasoline vapor during vehicle fueling and return the emissions to the gasoline storage tank. ORVR equipment also controls the release of hydrocarbon emissions during vehicle fueling by collecting the vapor into a canister in the vehicle. Therefore, the amount of displaced gasoline vapors meant to be captured by Stage II Vapor Recovery systems is being eliminated as more vehicles equipped with ORVR replace older vehicles. Additionally, the two systems are actually incompatible with each other since use of Stage II Vapor Recovery on a vehicle equipped with ORVR can actually cause more emissions to be released into the atmosphere.
Therefore, states in the Northeastern US have begun using several EPA criteria to classify that ORVR is in “widespread use” throughout their state. These states have begun to phase-out or discontinue the requirement for Stage II vapor recovery systems at gasoline dispensing facilities (GDFs). The phase-out of Stage II vapor recovery is good news for GDF owners and operators because the Stage II systems can be complicated and require periodic testing and upkeep that is expensive.
The state of Connecticut is currently moving forward with steps to repeal their requirements (see ECS Eclipse article dated January 3, 2012: http://www.ecseclipse.com/post-details/items/connecticut-moving-to-repeal-the-stage-ii-vapor-recovery-requirements.html).
Other states have already amended their regulations to phase-out Stage II systems. Here are details for some Northeastern US states that have regulations updated to allow discontinuing Stage II.
Chapter 118 of the state of Maine’s air rules was amended on April 3, 2011. Stage II requirements have been repealed as of January 1, 2012. GDFs with Stage II must discontinue the use of and/or remove the Stage II system by January 1, 2013, in compliance with Appendix A of Chapter 118. Previous rule amendments allowed that new facilities constructed on or after June 30, 2008 and facilities that exceeded the throughput requirements which would have made them subject to Stage II after January 1, 2008, did not need to install Stage II systems.
In New Hampshire, changes to Env-Wm 1404.17 were effective on November 29, 2011. New facilities constructed after January 1, 2012 or facilities where Stage II equipment had not already been installed, are no longer required to install Stage II systems. Stage II systems can be decommissioned starting after January 1, 2012, and must be decommissioned by December 22, 2015.
The state of Vermont enacted a law in 2009 (10 V.S.A. 583) that authorizes the phase-out of Stage II systems. New facilities that began operation after May 1, 2009 and facilities that did not exceed the throughput threshold (requiring Stage II installation) before the 2009 calendar year were not required to install Stage II systems. Owners or operators can discontinue the use of their Stage II systems after January 1, 2013. The systems must then be properly decommissioned by January 1, 2015, although the DEC encourages decommissioning to be done immediately after discontinuing the system. Early phase-out is allowed, but only in the cases where “significant excavation” is done or if all gasoline dispensers are replaced with dispensers that support triple data encryption standard usage to comply with payment card industry standards. Agency approval is required for early phase-out.
The state of New York has not yet repealed their Stage II requirements. However, the DEC issued a directive stating that the agency will use discretion in enforcement and will not issue violations for failure to comply with Stage II requirements at gasoline dispensing facilities that did not have a Stage II system prior to January 1, 2011 but were subject to the requirements after that date or for facilities that decommission their existing Stage II system after January 1, 2011 by following the procedure in Appendix A of the agency’s directive.
In order to decommission a Stage II system in one of these states, you must follow the state’s required procedures and approved methods. Generally, the agencies require advance notice or request for permission to decommission. Testing will be required and the Stage II piping is usually disconnected from the tank. The Stage II equipment, such as hanging hardware and pressure vacuum caps, must be replaced. The final step usually involves notification and/or submitting test reports to the agency.
Something to remember is that once a facility’s Stage II system has been decommissioned, gasoline dispensing facilities would then be subject to the federal National Emissions Standards for Hazardous Air Pollutants (NESHAP) - 40 CFR Part 63, Subpart CCCCCC. There would be additional equipment and sometimes testing requirements (dependent on gasoline throughput) associated with this regulation.
For more information, visit the following links:
ME: http://www.maine.gov/dep/air/rules/index.html (Chapter 118)
NH: http://des.nh.gov/organization/commissioner/legal/rulemaking/documents/env-wm1404.17as-amd.pdf
VT: http://www.anr.state.vt.us/air/Compliance/htm/Gasoline.htm
NY: http://www.dec.ny.gov/regulations/74990.html
- Megan Kazmierczak
Senior Compliance Manager
Paperwork Disorganization
January 6, 2012 (comments: 0)
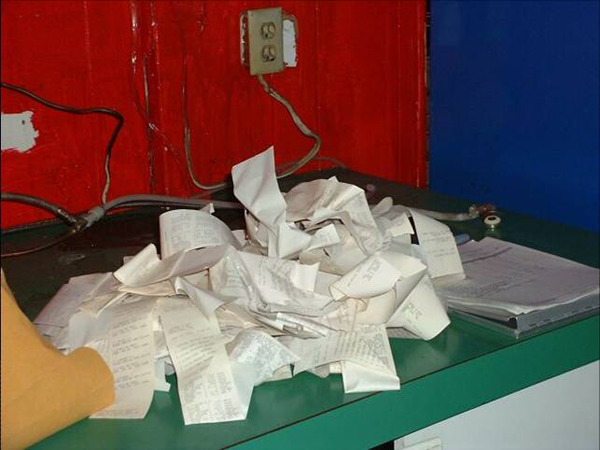
I have done a fair share of facility inspections and compliance audits throughout the years. One of the most common themes I have run across is disorganization of paperwork. The last few years have seen an increase in the number of Notices of Violation and penalty fines to the gasoline retailers targeted by the Regulatory Agencies. This increase of NOV’s and fines is due generally to an increase of focus on compliance which leads to an increased number of facility inspections. One of the most common violations includes the Monthly/Weekly Release Detection record keeping. These are the printouts generated from your automatic tank gauging system. Some of the tasks a State Regulator will do will be to - Unexpectedly arrive at your facility - Review all required paperwork including the release detection records - Observe the general condition of the facility - Ask the operator questions.
Organization is a key factor. Keeping your records organized, in chronological order and accessible goes a long way towards avoiding any fines. Typically if an inspector views the condition of the record keeping of release detection records as indicated by the photo, he will more apt to be dissatisfied and become increasingly critical during his inspection. This could potentially lead to NOV’s and fines. This is a common compliance issue that is a fairly easy fix.
There are many ways to do this. One is to place the monthly/weekly printouts in an envelope in chronological order by calendar year and save them in an accessible area for inspections. Another method that I was extremely impressed with was a retailer had purchased a three ring binder. The binder was clearly marked “Release Detection Records” Inside the 3 ring binder were collector card sleeves like the ones used to collect baseball cards. These clear plastic 3 ring sleeves each had 12 pouches that were used to hold the monthly release detection printouts by month. Each sleeve pouch was marked with month and year. And the 3 ring binder held 5 sleeves for the last 5 years. This doesn’t have to be your method, but you get the picture. Organization of record keeping is an easy way to avoid fines.
Third party management with remote monitoring of the automatic tank gauging systems is just one of ECS/eclipse’s specialties. We can take the headaches away. Please call for more information.
-Lorenzo DiBacco
Field Services Manager
The End of Ethanol?
January 3, 2012 (comments: 0)
On January 1, 2012, the federal subsidy for corn-based ethanol expired. Most of us have
become accustomed to labels on fuel dispensers indicating the percentage of ethanol in
gas being pumped. Many fuel dispensing facilities in the Midwest, where most ethanol
production occurs, have undertaken equipment upgrades to allow for retailing E85, with
85% ethanol. During the last 3 decades, roughly $20 billion in taxpayer funds have
gone to ethanol producers. Does the end of this subsidy mean the end of ethanol in our
gasoline?
Bruce Babcock of Iowa State University said in an interview on NPR, “Corn ethanol is
really the only lower cost substitute [to gasoline or crude].” As long as the price of oil
remains high, suppliers will continue to buy ethanol as a low cost substitute to gasoline.
So, it appears that ethanol in our gas is here to stay along with all of the considerations
that one must make with respect to dispensing ethanol.
-Brian Yellan, ECS Eclipse Trainer
Connecticut moving to repeal the Stage II Vapor Recovery Requirements?
January 3, 2012 (comments: 0)
Most of you are familiar with the Stage II rules and regulations as it relates to the equipment and activities at gasoline dispensing facilities. Under the Clean Air Act, Stage I and II was established to minimize Volatile organic compounds (VOC) and hazardous air pollutants (HAP) VOC emissions to the atmosphere. VOCs and HAPs are emitted from the refueling of light-duty gasoline vehicles and trucks (hereafter referred to as vehicles) at gas stations or, more formally, gasoline dispensing facilities (GDF) and from fugitive sources at GDF.
Controlling these emissions has been an issue for all stakeholders involved in the reduction of ozone and the production and dispensing of gasoline since the late 1980s. VOC and HAP emissions occur from two types of sources at GDF: Stage I and Stage II processes. Stage I refers to processes at GDF when the gasoline is delivered or transferred from the tanker truck to the underground storage tank (UST). Stage II refers to processes at a GDF when the gasoline is delivered or transferred from the UST to the vehicle fuel tank. Emissions from Stage II processes are the focus of this article. Stage I processes are mentioned only for clarity. Emissions from GDF are a nationwide problem, and gasoline use in vehicles and trucks is increasing annually however there has been a fundamental movement to eliminate the requirements for Stage II regulations. The reason is that the automotive manufacturers have been installing an on-board refueling vapor recovery (ORVR) canisters for over a decade, (ORVR will be used forward in this article). Basically the ORVR system in essence reclaims the vapor emission during the vehicle fueling process, negating the need for the complex and costly Stage II equipment at GDFs.
Eventually, given enough vehicles in use in the United States equipped with ORVR, technically Stage II equipment at the GDF is no longer required. In fact, continuing to have Stage II equipment during the fueling process for vehicles that have ORVR can actually CREATE and exasperate the emissions problem. CARB (California Air Resource Bureau) predicts that, as a result of ORVR/vacuum assist system incompatibility, “up to 35% efficiency loss could occur [in assist system control efficiency] based on theoretical calculations.”
The Clean Air Act (CAA) Section 202 (a) (6) states, with respect to ORVR requirements, “The requirements of Section 7511a (b) (3) of this title (relating to Stage II gasoline vapor recovery) for areas classified under Section 7511 of this title as moderate for ozone shall not apply after promulgation of such standards…”
The general interpretation of this is to indicate that states with Stage II programs in Moderate ozone nonattainment areas, as well as Marginal and attainment areas in the Ozone Transport Region (OTR), may begin to phase out their Stage II programs. The Northeast states are beginning to feel pressure to repeal their Stage II programs, as in the state of Maine, which essentially has begun the process of Stage II phase out process quite some time ago as well as other states.
According to CAA Section 202 (a) (6), the EPA Administrator may repeal the federal requirement mandating Stage II vapor recovery programs upon determination that vehicles equipped with ORVR systems are in “widespread use.”
On the question to the definition of “widespread use,” the EPA took a position as a guidance to all States that such a determination would be based on “the percentage of the automobile fleet equipped with ORVR.” To most industry stakeholders, this suggested that “widespread use” would occur when ORVR achieves emissions reductions on a one-to-one basis when compared to Stage II. For heavily populated areas with strong economic “engines” such as the Northeast, that time is already here.
Connecticut is now one of the Northeast states moving forward to establish a phase out of Stage II requirements however they are potentially looking to “beef up” the Stage I requirements but I question why……….As far as Stage I, I’m surprised CT would even pursue tougher standards given already a pretty tough federal standards under
National Emissions Standard for Hazardous Air Pollutants (NESHAP), Subpart CCCCCC
Traditionally Connecticut moves relatively slowly as it relates to reg. changes but there is a keen interest by the impacted stakeholders, namely the owner/operators in CT wishing to see this come to pass quickly.
- Joel Hershey, Director
Post Tags
- 24/7
- alarms
- ATG
- ATG monitoring
- August 8 2012
- Automatic tank gauge
- buying a convenience store
- Buying Station
- Cleanup Fund
- Cleanup Program
- Compliance
- compliance audits
- Connecticut
- construction
- credit card
- CT
- Decommissioning
- DEEP
- Dispensers
- Double Wall piping
- Draft UST Regulations
- DW Piping
- EPA
- Ethanol
- Facility Compliance
- facility inspections
- Fuel Spill
- Fuel Theft
- gasoline
- Gas Station
- Gas Station Inspections
- gas station tanks
- Identity Theft
- Independent Oil Marketers Association
- Inspection
- inspections
- interstitial monitoring
- inventory reconciliation
- IOMA
- MA
- MA DEP
- manways
- Massachusetts
- MA UST
- MA UST Regulations
- NH UST Regulations
- Notice of Violations
- NOV
- NOV's
- Ohio
- Operator Training
- Organization
- permanent tank closure
- Petroleum
- Recordkeeping
- Regulations
- release detection
- remote monitoring
- Rhode Island
- secondary containment
- Selling a convenience store
- Selling Station
- sensors
- Shear Valve
- single wall tanks
- Single wall ust closure
- Spill Bucket
- Stage II
- Stage II Decommissioning
- Stage II Vapor Recovery
- State Fund
- State Regulations
- storage tanks
- SW Closure
- tank regulations
- Tightness Testing
- underground piping
- underground storage tank
- Underground Storage Tank Regulations
- underground storage tanks
- UST
- UST's
- UST Compliance
- UST Inspections
- UST Operator Training
- UST paperwork
- UST Regulations
- UST removals
- UST Rules
- UST Training