1.888.302.4875
ECS Eclipse News Archives August 2012
Skimming for Skimmers
August 15, 2012 (comments: 0)
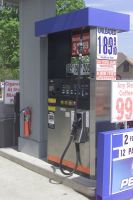
When most regulated storage tank system owners, operators, and contractors think of performing an inspection of a motor fuel dispenser, they think of inspecting for environmental compliance and maintenance. They look for leaks, drips, broken or warn out equipment, and other items that may pose certain risks. This type of inspection is typically required to be performed due to regulatory requirements from certain agencies having jurisdiction over the tank system. The purpose of these inspections is to ensure the safety and well being of people and the environment.
But, when it comes to people, there may be another danger associated with the use of motor fuel dispensers. One not directly associated with leaks, spills, fire, or physical safety, but one that can still cause devastation; IDENTITY THEFT.
Identity theft is something that seems to occur more and more often as our world becomes increasingly technologically advanced. In an age of widely used credit cards, debit cards, and other electronic payment methods, our personal information can be at risk of falling into the wrong hands. It isn’t news to anyone that care must be taken when using a credit or debit card to pay for something over the internet, but very few people think twice about swiping their card at the pumps.
Identity theft at motor fuel dispensers occurs in a way that is different from internet purchases. It is not necessarily a matter of hackers getting through website security or using software to retrieve credit card information, but the physical installation of “skimmer” devices on the gas pump card readers.
Most people have a basic understanding of how a credit card transaction works at a gas pump. The customer inserts or swipes a card through a card reader device, which then reads the necessary account information to make the transaction from the card’s magnetic strip. By installing a foreign device called a “skimmer” in place of or attached to the existing card reader, identity thieves can attain this same information.
The nature of a motor fuel dispenser makes it an ideal target for identity thieves. Credit card readers are used almost anywhere a purchase can be made. Typically they are under close supervision from clerks, attendants, and other personnel, such as those located at a cash register in a supermarket. But card readers located outdoors at gas pumps are not always directly supervised. This provides thieves with an opportunity to tamper with these devices, unnoticed.
So the big questions is; “How do I know if a skimmer has been installed?” The answer however, may not be so simple. Outside of the obviously tampered, flimsy, and unofficial appearance some cheaper external skimmers may have, it may be impossible for the average customer to know the difference before making a purchase. Higher quality skimmers can have an appearance indistinguishable from the original card reader. Some skimmers are even installed on the dispenser internally and use the factory card reader.
Owners and operators on the other hand, are in a position where they can become more familiar with their equipment, making identification of a foreign device more feasible. Performing inspections regularly can help owners and operators get to know their equipment, and be able to spot anything out of the ordinary. Though contractors performing maintenance work or inspection of a dispenser may not have the same day to day familiarity with the specific facility, their experience and expertise gives them the ability to identify such devices.
As discussed earlier, many owners and operators of storage tank and dispenser systems are already required to perform regular environmental compliance and maintenance inspections. So, while you are there, don’t just skim through the inspection, inspect for the skimmers. It could save someone’s identity.
- Troy Dickins, Field Services Technician
Changes to Stage I and II Vapor Recovery in Massachusetts
August 9, 2012 (comments: 0)
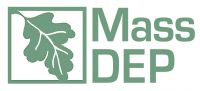
Changes to Stage I and II Vapor Recovery in Massachusetts
UST owners or operators in Massachusetts should have recently received a postcard from the MassDEP regarding changes to Stage II Vapor Recovery Requirements. The reason for the change is that on May 16, 2012, the US EPA issued a rule allowing states to phase out their Stage II Vapor Recovery programs. You can read a full letter about the Massachusetts Stage II Enforcement Discretion from the MassDEP Commissioner here: http://www.mass.gov/dep/air/laws/s2ltr12.pdf
The Massachusetts change was effective July 9, 2012 and the MassDEP is now using enforcement discretion to no longer require “installation Stage II Vapor Recovery systems under 310 CMR 7.24(6) at the following facilities:
- A new motor vehicle fuel dispensing facility dispensing gasoline for the first time.
- An existing facility where:
- there is excavation below a shear valve or tank pad to repair or replace a Stage II system or an underground storage tank; or
- 50 percent or more of the dispensers are replaced; and
The entire Stage II system is fully decommissioned in accordance with applicable guidance.”
Unless one of the conditions described above occurs, owners and operators must continue to operate and maintain their Stage II system in accordance with regulations. If the Stage II system is decommissioned or in the case of a new facility without Stage II, owners and operators must comply with Stage I Vapor Recovery requirements. The Stage I requirements include performing visual inspections, maintaining records, submitting annual compliance certifications and paying annual fees. Annual Stage I testing (pressure decay, vapor tie and pressure/vacuum vent test) must also be performed.
In speaking with the MassDEP, we learned that the Stage I program will be very similar to the existing Stage II program. The MassDEP is still in process of developing the forms and process, but the annual compliance certification will be a Form C for Stage I, like the Stage II Annual In-Use Compliance Certification Form C. For new installations or if the Stage II system was decommissioned during excavation (see condition 2.a. above), a Stage I Form A will be required. For sites where Stage II is decommissioned, the MassDEP plans to use the existing Stage II certification due date to act as the Stage I annual compliance certification due date.
The MassDEP’s frequently asked questions (http://www.mass.gov/dep/air/community/s2edfaq.htm) can provide further details about the process for decommissioning Stage II systems, documentation required for decommissioning and about the Stage I Vapor Recovery requirements.
- Megan Kazmierczak, Senior Compliance Manager
Post Tags
- 24/7
- alarms
- ATG
- ATG monitoring
- August 8 2012
- Automatic tank gauge
- buying a convenience store
- Buying Station
- Cleanup Fund
- Cleanup Program
- Compliance
- compliance audits
- Connecticut
- construction
- credit card
- CT
- Decommissioning
- DEEP
- Dispensers
- Double Wall piping
- Draft UST Regulations
- DW Piping
- EPA
- Ethanol
- Facility Compliance
- facility inspections
- Fuel Spill
- Fuel Theft
- gasoline
- Gas Station
- Gas Station Inspections
- gas station tanks
- Identity Theft
- Independent Oil Marketers Association
- Inspection
- inspections
- interstitial monitoring
- inventory reconciliation
- IOMA
- MA
- MA DEP
- manways
- Massachusetts
- MA UST
- MA UST Regulations
- NH UST Regulations
- Notice of Violations
- NOV
- NOV's
- Ohio
- Operator Training
- Organization
- permanent tank closure
- Petroleum
- Recordkeeping
- Regulations
- release detection
- remote monitoring
- Rhode Island
- secondary containment
- Selling a convenience store
- Selling Station
- sensors
- Shear Valve
- single wall tanks
- Single wall ust closure
- Spill Bucket
- Stage II
- Stage II Decommissioning
- Stage II Vapor Recovery
- State Fund
- State Regulations
- storage tanks
- SW Closure
- tank regulations
- Tightness Testing
- underground piping
- underground storage tank
- Underground Storage Tank Regulations
- underground storage tanks
- UST
- UST's
- UST Compliance
- UST Inspections
- UST Operator Training
- UST paperwork
- UST Regulations
- UST removals
- UST Rules
- UST Training